To get the most out of the machine and its performance vibration sensors are used. It is used to monitor parameters like speed, temperature, and vibration of the machines that are working continuously. If these parameters are not monitored regularly it can impact negatively on the health of machines. It becomes more crucial to track these parameters for commercial and businesses. The negligence can result in machine damage and downtime for maintenance that will impact the finances.
Among other parameters for optimum functioning of machinery, vibration is such an element. We are going to discuss further why vibration sensors are used and what is the application of the vibration sensors along with the vibration sensor working principle.
Vibration Sensor
The vibration sensor can be described as a machine or an electromechanical device that brings balance to the position of machines. Vibration is something that creates mechanical oscillation and distorts the equilibrium and position of the components and machines.
To put it simply, the machines get rocked back and forth due to the motion of a machine or component.
Vibration in the machinery and industrial equipment is considered normal operation and part of the functioning but sometimes it can create issues and become a signal of maintenance requirement and upkeep.
There are two primary types of vibration in industrial machines:
Axial/Thrust Vibration & Radial Vibration
In axial vibration is seen in the longitudinal shafting or parallel shaft in the motor. For example, the alignment change in the shaft of the motor is known as axial vibration.
The radial vibration happens when the force is applied from outside towards the shaft of the motor. Radial vibration happens when a heavy part rotates in the motor during action time.
Best Offer Available
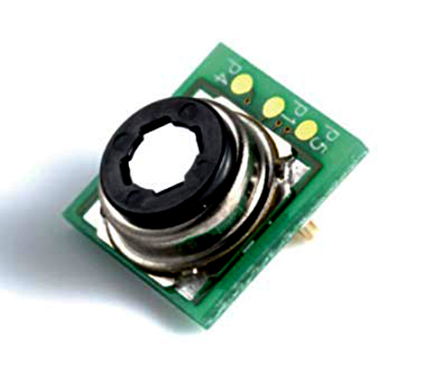
Omron D6T-1A-02 MEMS Thermal Sensors
Request For Price
Omron D6T-1A-01 MEMS Thermal Sensor
Request For Price
What is the purpose of monitoring vibrations?
Any industry that uses heavy machinery for their daily working and operations needs regular monitoring of vibration as it can be advantageous for many reasons:
It can help to understand the causes of damage
The vibration monitoring will help in root cause analysis of machinery when the equipment is showing signs of slowing down and needs upkeep. It will also help to determine the cause of the damage if more action is required.
It also monitors repair and maintenance
Vibration monitoring is best for preventing action and maintenance. The vibration analysis tracks the real-time performance of the machines. If the vibration is increased and reaches a dangerous level that is reflected in the monitored data. By this, it can be predicted when the machinery requires maintenance.
Keep an overall health check on the equipment
The monitoring of machines and conditions is based heavily on sensors and this is not different from vibration sensors. If the assets of the organization are monitored, their work and working life cycle can be predicted.
Vibration Sensor Working Principle
The working principle of the vibration sensor is based on different mechanical principles for proper detection of observing the vibrations of machinery.
The vibration sensors have high sensitivity that ranges from 10 mV/g to 100 mV/g. the high and low points of these sensors for different levels of sensitivity can be adjusted and are also accessible. The sensitivity can be selected according to the specific applications.
To work these sensors properly it is necessary to know the levels of vibration and the amplitude range. The vibration sensor will be exposed to these ranges throughout the measuring times and process of operation.
How do Vibration sensors work?
This sensor works in three types of the basic functioning of displacement, velocity, and acceleration.
The displacement monitors the changes between a machine’s rotating element and its stationary distance. The displacement sensors come with the probe that is inserted into the hole that is drilled accordingly and hooked up on the machine’s outer layout. This probe is situated above the surface of the rotating shaft of the machinery that is being measured.
The velocity and acceleration work in an opposed manner. It monitors the velocity and acceleration of the attached external part of the machine layout.
Applications of vibration sensor
The application of vibration sensors ranges from different industries. Many different types of industries use the Omron vibration sensors for measuring different parts of the machines. The particular industrial characteristics and uses can be decided by the exact applications.
The vibration sensor is required in wind power and mining industries to measure the slow rotation of turbines with a 1 Hz or lesser frequency rate.
On the other hand, it is also used in gas and oil where it measures the high frequency that ranges from 10 Hz to 10 kHz. The oil & Gas industry uses vibration sensors to manage the rotation speed of gears and turbines.
The major industries that have used Omron vibration sensors are food & beverage, mining, metal fabrication, gas & oil, paper, wind power, power generation, etc.
Conclusion
Vibration sensors are an extremely good manner to display the fitness of key assets. They offer particular statistics on how personal portions of the gadget are doing, and the records they offer allow you to expect while destiny upkeep wishes may also occur. The quiet result is a greater streamlined upkeep technique and advanced system fitness.
A vibration sensor is a tool that measures the quantity and frequency of vibration in a given system, system, or piece of gadget. Those measurements may be used to stumble on imbalances or different troubles in the asset and are expecting destiny breakdowns.